Closed Loops
Chemical Treatment of Closed Loops is an often over-looked, but highly valuable part of facility maintenance. Dirty, neglected loops can cause massive disruptions in heating and cooling systems resulting in down-time and costs for cleaning and disinfection. A full-service water treatment program with Metro Group monitors the health and operating efficiency of these systems.
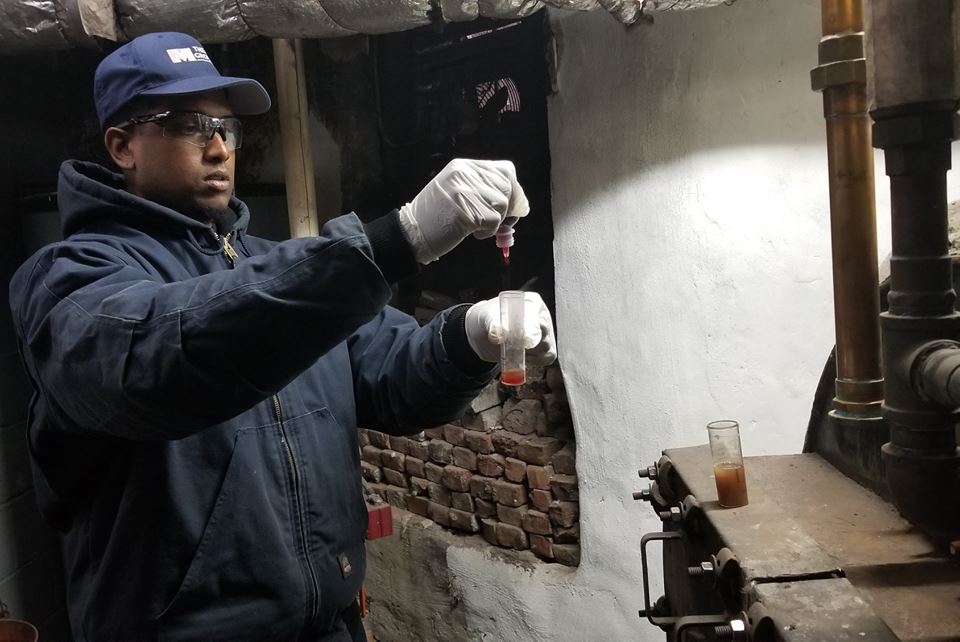
Monitor and Control the Water Chemistry in Closed Loops
Regular visits provide the facility with a second set of eyes on their mechanical systems, and the detection of leaks and low chemical levels can alert you of problems before they become catastrophes. It’s important to closely monitor and control the water chemistry in closed loop, hot and cold, re-circulating systems because corrosion and microbiological fouling impact heat exchange even in systems experiencing relatively modest water loss. If left unchecked, corrosion and bio fouling will shorten the useful life of piping, valves, and heat exchangers in these systems. See Side Stream Filtration.
- Closed loop systems distribute heated or chilled water throughout a building, with water temperatures ranging from 42° F to 250° F and water velocities between 2 and 5 feet per second. Process water loops often experience much higher temperatures and velocities as much as 10 feet per second. Closed loop HVAC systems typically contain several types of metallurgy including mild steel, cast iron, copper, brass, and aluminum. A water treatment program must protect all of these metals.
- Effective closed loop treatment programs utilize a blend of corrosion inhibitors, scale control agents, and microbiocide, and the necessary field service to insure good control of system chemistry. See also Loop Cleaning.
Full-Service Water Treatment Program’s with Metro Group are designed to protect and optimize valuable capital equipment while taking the burden off facility personnel. Full-Service programs eliminate chemical handling by facility personnel and reduce the amount of chemical required to be stored. Regularly scheduled service visits include water parameter testing with electronic reporting, program adjustment, chemical inventory control, and calibration and programming of feed & control equipment.